Системы автоматического оптического контроля монтажа печатных плат
Tyco Electronics Automation Group
Многое изменилось с тех пор, как первые системы технического зрения были представлены на рынок в начале 80-х годов прошлого века. Теперь такие системы стали называть системами автоматического оптического контроля (Automated Optical Inspection — AOI). Совсем недавно рынок оборудования AOI, имея более 30 поставщиков, не был точно определен. Большинство их потенциальных потребителей не обладало достаточными знаниями о технологии оптического контроля, чтобы использовать ее в производстве. Автоматизированный оптический контроль получил плохую репутацию, так как многие системы работали некорректно. Бытовало мнение, что никогда не будет системы, которая отвечала бы всем требованиям промышленного производства, быстрого программирования, высокой производительности и обладала бы низкими показателями отказов и ошибок. В большинстве систем все еще применялась технология корреляции полутонов (Grey Scale Correlation), которая имела ряд очевидных недостатков, но альтернативы не было. С 1996 года ViTechnology (Dyamant) начала работать с компанией Cognex (США) — мировым лидером в поставке программного обеспечения для систем оптического контроля и аппаратных средств (ViTechnology входит в состав Tyco Electronics Automation Group).
Используя некоторые новые решения от Cognex, ViTechnology развивает новую технологию под названием Vectoral Imaging™ Technology (технология векторных изображений), которая произвела революцию в секторе AOI-оборудования. Преимущества Vectoral Imaging были ясны с самого начала: система использовала синтетические модели, которые не были связаны с окружающей средой, и поэтому не зависели от изменений цвета, фона или освещения. Технология Vectoral Imaging позволяет не только определять присутствие, отсутствие и полярность установленных компонентов, но также измерять отклонения по координатам X, Y и по координате вращения q, поскольку обеспечивает анализ вращения.
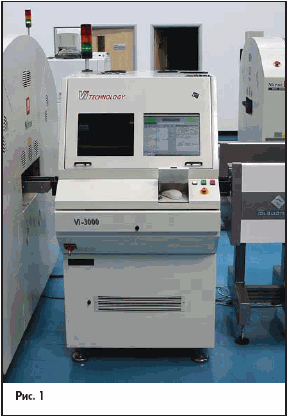
В то же время система способна осуществлять точные измерения на уровне подпикселей. С 1999 года компания ViTechnology продвигает на рынок систему автоматического оптического контроля Vi-3000 (рис. 1), которая может использоваться в поточной производственной линии не только после операции оплавления припоя для обнаружения дефектов, но и перед печью оплавления припоя, а также после операции нанесения паяльной пасты — чтобы выявить дефекты прежде, чем они окажут неблагоприятное воздействие на процесс. По мере того как ViTechnology продолжала продвигать новую технологию и само использование систем AOI, все больше скептиков убеждались, что системы AOI должны использоваться после операции оплавления припоя для оптического осмотра не только компонентов, но и паяных соединений, формы контактных дорожек, а также определения размера и качества паяных соединений. Теперь не стоит вопрос, стоит ли применять системы автоматического оптического контроля. Главный вопрос — где их применять? Если производитель желает избежать затрат, связанных с возвратом бракованных изделий, то применение системы AOI в конце производственной линии является вполне логичным. Но проблема в том, что в этом случае такая система не обеспечивает всестороннего анализа. Дополнительно требуется система рентгеновского контроля, которая обеспечивает контроль качества паяных соединений, а также выявляет их наличие. Применение системы оптического контроля в конце производственной линии не исключает затрат на переделку бракованных изделий, которые могут быть значительно минимизированы в случае применения AOI для мониторинга результатов каждой операции производственного процесса. Производственная линейка, укомплектованная системами автоматического оптического контроля для предотвращения брака, выполняет операции, представленные в таблице 1. Если не брать в расчет затраты на организацию этой линии, такое размещение систем автоматического оптического контроля, предотвращающее возникновение брака, считается оптимальным. Такая стратегия базируется на философии мониторинга процесса или предотвращения брака и требует внедрения до 9 систем AOI.
Таблица 1
Обработка платы с одной стороны |
Обработка платы со второй стороны |
Трафаретный принтер или автомат диспенсорного нанесения паяльной пасты |
Трафаретный принтер или автомат диспенсорного нанесения паяльной пасты |
AOI |
AOI |
Установщик чипов |
Установщик чипов |
AOI |
AOI |
Установщик компонентов с малым шагом выводов |
Установщик компонентов с малым шагом выводов |
AOI |
AOI |
Печь оплавления припоя |
Печь оплавления припоя |
AOI |
AOI |
Установка для монтажа компонентов в отверстия |
Установка пайки волной |
|
AOI |
Применение системы AOI после автомата установщика компонентов с малым шагом выводов обеспечивает выявление ошибок, связанных с работой автомата. Однако отсутствует мгновенная обратная связь, посредством которой можно подкорректировать его работу. Ключевая проблема — обеспечение передачи информации сразу же после выполнения определенной производственной операции, чтобы возможный сбой был вовремя отслежен и были предприняты соответствующие корректирующие действия, прежде чем брак достигнет крупных масштабов. Если для обработки с другой стороны платы перенаправляются через те же самые автоматы-установщики, то требуется только 5 систем AOI.
Если в производственном процессе нет операции пайки волной, то всего 4. Таблица 2 отражает выявляемые типы дефектов в зависимости от места применения системы AOI.
Таблица 2
Тип дефекта |
После принтера трафаретной печати |
После установки компонентов |
После операции оплавления припоя |
После операции пайки волной |
Недостаточное нанесение паяльной пасты |
х |
х |
|
|
Блокированные отверстия |
х |
х |
|
|
Короткое замыкание (паста) |
х |
х |
|
|
Смещение пасты |
х |
х |
|
|
Пропущенный компонент |
|
х |
х |
х |
Перекошенный компонент |
|
х |
х |
х |
Полярность |
|
х |
х |
х |
Смещение компонента |
|
х |
х |
х |
Установлен не тот компонент |
|
х |
х |
х |
Отогнутый или сломанный вывод |
|
х |
х |
х |
Избыточное количество пасты |
|
|
х |
х |
Вздыбливание компонентов |
|
|
х |
х |
Непропаянное соединение |
|
|
х |
х |
Короткое замыкание после операции пайки |
|
|
х |
х |
На основе этой таблицы можно провести анализ дефектов и частоту их возникновения в определенной производственной линии и сделать вывод, в каком месте применение систем AOI наиболее оправдано, определить какие дефекты система должна выявлять и какие дефекты она могла бы выявить. Другими словами, результатом анализа будет соотношение желаемого и необходимого.
Внедрение замкнутого контура управления процессом посредством применения систем автоматического оптического контроля в производстве обеспечивает не только улучшение качества изделий и производительность всей линии, но и экономию средств, несмотря на то, что эти системы относительно дорогостоящи. В расчет включается экономия средств от оплаты труда производственным рабочим, затрат на исправление брака, затрат на осуществление гарантийного ремонта, оплаты труда вспомогательных рабочих, связанных с осуществлением оптического осмотра, затраты на обучение операторов и стоимость ремонтного оборудования. Это достаточно большая сумма, если учесть, что в развитых странах, например, рабочее место оператора, осуществляющего визуальный осмотр, должно быть оснащено дорогостоящей эргономичной рабочей станцией. Таким образом, затраты на внедрение систем AOI окупаются в среднем за несколько месяцев.
Компания Tyco Electronics Automation Group предлагает широкий диапазон оборудования AOI фирмы ViTechnology, от начального уровня до профессиональных систем.
Библиотеки синтетических моделей позволяют клиентам быстро и эффективно программировать автомат, получая снижение вероятности отказов и возможность переносить модели и библиотеки с машины на машину. Эта гибкость также отражает возможность использования этих машин в любом месте поточной линии, одна и та же машина может использоваться для осмотра паяльной пасты до оплавления или после отверждения припоя, что очень важно для производителей, осуществляющих контрактное производство, которые изменяют планировку линии в зависимости от заказа и изделия.
Тот факт, что машины начального уровня могут быть модернизированы до полной Vi-3000 версии — главное преимущество для клиентов, которые, возможно, сегодня нуждаются в системе начального уровня, а завтра — в более полной системе. Все системы способны использовать ремонтные станции и системы автономного программирования. Системы Vi-3000, Vi-5000 и Vi-6000 могут использоваться с SPC-инструментами для анализа тенденций изменения параметров, а также могут импортировать файлы питателя и конфигурацию линии, чтобы отслеживать источники дефектов.
Особенности
- Оснащен технологией векторных изображений.
- Осмотр до 200 тыс. компонентов в час.
- Осмотр пасты в 2-х измерениях, площадок, регистрация координат XY, натеков и пустот.
- Селективный осмотр пасты в 3-х измерениях для измерения объема.
- Определение присутствия и отсутствия всех типов компонентов.
- Измерение положения в координатах X, Y и q для всех типов компонентов.
- Проверка полярности всех типов компонентов.
- Осмотр паяных соединений и быстрый осмотр схемы.
- Обнаружение непропаянных соединений и отогнутых выводов.
- OCV — способность считывать текст на поверхности компонентов.
- Полная SPC-совместимость (Statistical Process Control — сбор статистических данных о процессе).
- Малые габариты — возможность применения в любой производственной линии.
- Уникальное соотношение «цена — производительность».
- Одновременно с осмотром компонентов, уже установленных на плату, осматривает размещение пасты для компонентов с малым шагом выводов типа QFP, BGA, микро-BGA и всех компонентов типа флип-чип.
Осмотр после нанесения пасты
Производится оптический контроль контактных площадок на предмет точного нанесения паяльной пасты. С помощью различных режимов подсветки производится анализ смещения нанесенной пасты, выявляется недостаточное или избыточное количество пасты (рис. 2 и 3).
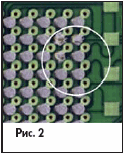 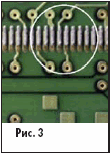
Осмотр после установки компонентов
Производится проверка на предмет присутствия и отсутствия компонентов. Анализируется точность установки и полярность (рис. 4), осуществляется оптический осмотр нанесенной пасты для компонентов с малым шагом выводов (рис. 5), CSP и BGA, а также производится проверка на предмет инородных предметов в этих местах (например, потерянных чипов) (рис. 6).
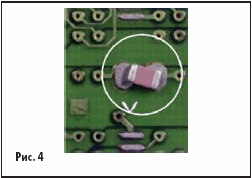
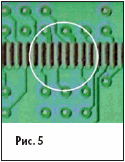 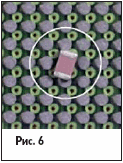
Осмотр после установки компонентов с малым шагом выводов
Проверка на предмет точности установки и правильной ориентации (рис. 7), а также выявление сломанных, отогнутых или скрученных выводов (рис. 8). Осуществляется оптическое распознавание маркировок на компоненте (OCV) для предотвращения некорректной установки дорогостоящих компонентов с малым шагом выводов или специальных компонентов (рис. 9).
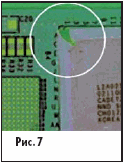 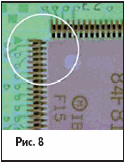
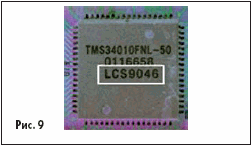
Осмотр после печи оплавления припоя
Производится анализ целостности паяных соединений для выявления непропаянных соединений, коротких замыканий (рис. 10), смещение за пределами допуска (рис. 12) или вертикальное поднятие одного края чипа в результате неравенства сил поверхностного натяжения пасты на контактных площадках при оплавлении припоя (рис. 11).
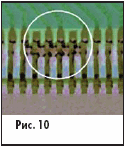 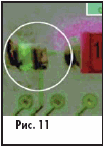
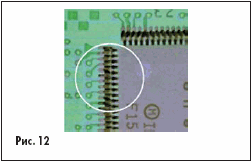
Дефекты могут возникнуть в любом месте производственной линии — на стадии нанесения паяльной пасты, установки компонентов, установки компонентов с малым шагом выводов и после операции пайки. Применение систем оптического контроля только в конце производственного процесса не является оправданным с точки зрения экономических затрат на эту систему, потому что единственный путь в этом случае — сложный и дорогостоящий ремонт. Решение этой проблемы — применение систем оптического контроля в определенных критических точках сборочной линии.
Высокая скорость и точность позиционирования
Для осуществления перемещений XY платформы применяются линейные приводы, не требующие обслуживания, и оптические кодеры с зеркальной шкалой. Точность системы ±10 микрон, повторяемость ±5 микрон в 6 сигма при скоростях до 2 м/с. Все электронные и механические узлы легкодоступны для осуществления профилактических и калибровочных работ.
Система подсветки
Система оснащена четырьмя различными программируемыми источниками освещения для получения максимально контрастного изображения. В процессе наладки системы оператор может выбрать любую из неограниченного количества комбинаций интенсивности осевой и пирамидальной подсветки и сочетания желтого и зеленого цветов для получения четкого изображения в самой сложной ситуации. Выбранная комбинация автоматически записывается в рабочую программу, которая управляет режимами подсветки в процессе производства.
Ремонтная станция
Ремонтная станция ViTechnology (рис. 13) может быть непосредственно связана с системами оптического контроля в производственной линии. Все ошибки, выявленные системами оптического контроля в процессе производства, выгружаются в ремонтную станцию в реальном времени вместе с реальными изображениями компонентов, установленных с браком. На графическом изображении всей платы отмечены места, где компоненты установлены с предельно допустимыми параметрами, либо требуется ремонт, либо это возможный «ложный сбой». Оператор видит изображения компонентов, принимает решение, какое действие предпринять, когда должен быть осуществлен ремонт, и отслеживает причину брака.
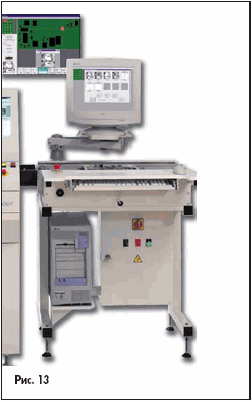
Затем эти данные заносятся в систему. Существуют различные конфигурации ремонтных станций и вспомогательных конвейеров в зависимости от применения и производительности линии.
Используя информацию штрих-кодов, ремонтная станция заносит в журнал все необходимые ремонтные операции с описанием и ратификацией ошибок.
Доступны специальные ремонтные станции, предоставляющие оператору возможность исправлять ошибки непосредственно в процессе производства или удалять изделия из производственной линии для последующего ремонта.
Для анализа изображений в системах автоматического оптического контроля применяется самое современное программное обеспечение Patmax, работающее под управлением Windows NT 4.0. В большинстве случаев система программируется за 15 минут с использованием данных Gerber, CAD или ASCII. Имеется встроенная обширная библиотека синтетических изображений компонентов, с которыми производится сравнение и анализ. Библиотека содержит изображения наиболее часто используемых компонентов, однако, по необходимости, изображения компонентов можно загружать из Интернета.
Все системы оптического контроля производственной линии могут быть связаны через сеть с ремонтной станцией и периферийным оборудованием для осуществления удаленного доступа и контроля.
Таблица 3. Vi.3000: Система автоматического оптического контроля (AOI) для плат стандартных размеров
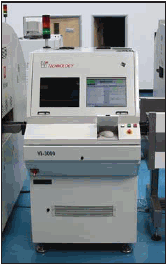 |
Особенности |
• До 200000 компонентов в час |
• Осмотр пасты в 2-х измерениях, площадок, возможных пустот и натеков |
• Определение присутствия и отсутствия всех типов компонентов |
• Позиционирование в координатах X, Y и q для всех типов компонентов |
• Полярность компонентов |
• Выявление паяных соединений с коротким замыканием |
• Выявление непропаянных соединений |
• Распознавание текста на поверхности компонентов |
• Осмотр может быть выполнен в любом месте конвейерной линии |
• Одновременный осмотр нанесенной пасты для компонентов с малым шагом выводов, таких как QFP, BGA, Micro BGA и Flip Chip |
• Цифровая камера Hitachi |
Автономная станция программирования
Дополнительная автономная станция программирования обеспечивает удаленное программирование в процессе работы систем оптического контроля. Станция оснащается патентованным программным обеспечением, позволяющим настраивать рабочую программу и вносить в нее изменения, а также создавать и изменять библиотеку синтетических изображений. В дополнение, сетевое программное обеспечение на системах оптического контроля и на ремонтной станции сконфигурировано таким образом, чтобы было возможно загружать
и выгружать рабочие программы, а также производить обмен SPC-данными между системами.
Конвертирование данных CAD
Дополнительное программное обеспечение для конвертирования данных CAD автоматически импортирует данные проектирования платы непосредственно в машинный формат, используемый в системах автоматического оптического контроля. Программное обеспечение для конвертирования включает в себя такие программные продукты, как UniCAM, CIMBridge, FABmaster и CircuitCAM, а также обрабатывает данные Gerber и ASCII.
SPC-контроль
Во все системы автоматического оптического контроля может быть интегрировано дополнительное программное обеспечение Lighthouse SPC (Statistical process control), которое обеспечивает непрерывный обмен информацией в реальном времени с программным обеспечением систем оптического контроля и позволяет проводить полный анализ производительности автоматов, отражать входящие и исходящие данные и делать анализ тренда. Функция увеличения позволяет взглянуть ближе на специальные позиции измерений с существенной информацией. Диаграмма Парето отражает частоту и дисперсию результатов измерений. Программное обеспечение работает под управлением Windows NT и обладает удобным графическим пользовательским интерфейсом с разграничением уровней доступа для оператора и технических специалистов, работающих с SPC-данными.
Дополнительную информацию можно получить на сайте www.automation.tycoelectronics.com/europe/
Андрей Астрицкий
|