Монтаж электронных модулей.
Используемое оборудование
Продолжение. Начало в № 5’2001.
Данная публикация продолжает тему монтажа электронных модулей и посвящена описанию технологического оборудования, входящего в состав сборочно-монтажного производства, и целесообразности применения того или иного оборудования в зависимости от характеристик монтируемого электронного модуля.
Рассмотрим факторы, которые оказывают влияние на выбор оборудования, его виды, производительность, на количество рабочих мест и другие характеристики производственной линии. Во-первых, общие особенности конструкции модуля, такие как номенклатура используемых компонентов, количество рабочих сторон модуля, на которых осуществляется монтаж, а также, в случае двустороннего монтажа, расположение компонентов: смешанно-разнесенное или смешанное.
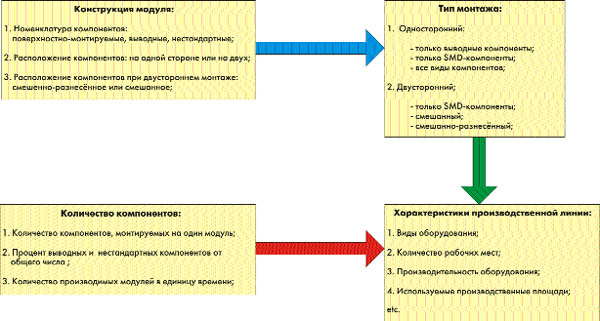
Зависимость состава производственной линии от характеристик модуля
Эти характеристики модуля оказывают влияние на выбираемый тип монтажа. Тип монтажа, в свою очередь, определяет виды оборудования, которое будет использоваться на производстве.
Во-вторых, на формирование производственной линии оказывают влияние количественные характеристики модуля:
- общее число монтируемых компонентов;
- количество выводных (Through Hole Technology, THT) и нестандартных компонентов (Odd Form Components);
- количество производимых модулей в единицу времени.
Эти параметры определяют необходимую производительность установленного оборудования и число используемых рабочих мест, на которых будут выполняться ручные операции.
Влияние описанных характеристик модуля на состав производственной линии отображено на рисунке.
Оборудование
Рассмотрим технологические операции, которые составляют производственный цикл, и оборудование, применяемое на каждом из них.
1. Загрузка и выгрузка плат
Необходимость использования автоматики для транспортировки плат, загрузки их в линию и выгрузки из нее определяется только масштабами производства. При изготовлении модулей в лабораторных объемах в таком оборудовании нет необходимости. Даже при серийном производстве с небольшой производительностью затраты на автоматическую транспортировку вряд ли будут оправданы.
Автоматические загрузчики и транспортные системы целесообразно использовать только на крупносерийном производстве, где используется автоматическая линия и весь процесс расписан посекундно. В таких условиях автоматическая транспортировка сильно упростит задачу и сэкономит время.
2. Нанесение материалов
Как правило, технологический цикл сборки электронных модулей начинается с нанесения на поверхность печатной платы материалов (паяльной пасты или клея). Общеизвестны два способа выполнения этой операции: трафаретная печать и дозирование.
Если на производстве изготавливается большое число конструкций плат, то целесообразно применять метод дозирования, особенно при лабораторном производстве, когда на оборудование, ввиду его невысокой производительности, были потрачены сравнительно небольшие финансовые средства. В случае применения трафаретной печати необходимо использовать по одному трафарету на каждую сторону каждого конструктива платы, что потребует введения на производстве новой операции по изготовлению трафаретов или их покупки. Стоимость трафарета составляет $200–600 за штуку. При большом их количестве себестоимость обработки существенно увеличится, несмотря на то, что стоимость самого оборудования не слишком высока.
В случае промышленного производства, напротив, нанесение материалов методом дозирования нежелательно из-за низкой скорости и стабильности процесса по сравнению с трафаретной печатью. К тому же на крупносерийных производствах число выпускаемых конструкций плат ограничено, да и стоимость трафаретов не внесет заметного вклада в общие расходы ввиду высокой стоимости оборудования.
Теперь рассмотрим устройства трафаретной печати. Они могут быть как ручными, так и автоматическими.
Ручной принтер представляет собой сравнительно простое устройство: на металлической раме закрепляется трафарет, после чего раму крепят к рабочему столу, на котором находится плата. Для лучшего соприкосновения платы и трафарета в пространстве между ними может быть создано низкое давление. Для этого дополнительно используют вакуумный насос. При использовании ручного принтера давление на ракель осуществляется оператором вручную.
В автоматических принтерах все операции — совмещение трафарета и печатной платы, осуществление приводного давления на ракель, дозирование припойной пасты на трафарет — выполняются автоматически. Эти устройства могут работать как автономно, так и в составе производственной линии. В зависимости от класса этого оборудования оно может выполнять различные дополнительные функции, такие как автоматическая инспекция печатной платы при помощи технического зрения, приводное изменение ширины конвейера и другие.
Основные параметры автоматических принтеров: максимальный формат платы, который может достигать значения 510ґ510 мм, и скорость перемещения ракеля (до 150 мм/с).
При использовании автоматического принтера в промышленной линии особое значение приобретают возможности программного обеспечения (ПО), которое на нем установлено. В наиболее высококлассном и дорогостоящем оборудовании ПО позволяет устройству получить доступ к централизованной базе данных предприятия, подключаться к локальной сети и даже использовать Интернет для удаленного доступа. Все это позволяет оборудованию повышать качество изделий и уменьшать количество ошибок.
Другой вид оборудования для нанесения материалов — устройства дозирования. Как уже отмечалось, такое оборудование рационально использовать только в случае невысокой производительности монтажного участка, при лабораторном характере производства. Поэтому такое устройство нет необходимости встраивать в автоматическую линию. Автоматический дозатор представляет собой рабочий стол, на который крепится обрабатываемая плата. Над рабочим полем автоматически перемещается дозатор, который осуществляет нанесение материалов на плату. Для управления используется персональный компьютер и относительно несложное специальное ПО.
Ключевые параметры автоматических дозаторов: скорость дозирования (до 15 тыс. точек в час) и максимальный формат обрабатываемой платы (до 450x450 мм).
Для нанесения материалов можно применять и ручное дозирование. Однако это рацио-нально только при очень невысокой производительности монтажного участка, так как у оператора производительность, естественно, существенно ниже, чем у любого из описанных выше видов оборудования.
3. Установка компонентов
Установка компонентов является, пожалуй, наиболее важной и сложной операцией в технологическом цикле. Как правило, именно производительность установки компонентов на плату определяет общую производительность монтажного участка.
Наиболее простой и наименее производительный метод установки компонентов — ручной, при помощи соответствующего инструмента. В этом случае большую роль играют субъективные факторы, такие как уровень профессионализма и опыт оператора. Кроме того, при использовании некоторых современных компонентов вероятность ошибки оператора увеличивается. Установка наиболее сложных компонентов (маленьких чипов 0102 и fine-pitch) отнимает у оператора много времени, а для установки компонентов в корпусах BGA необходимо специальное оборудование.
Следующим по производительности способом установки компонентов является полуавтоматический монтаж на специальной установке. Спектр оборудования, предлагаемого различными фирмами, достаточно широк, но в целом устройство таких установок одинаково. Установка состоит из рабочего поля, на котором закрепляется плата, над ней в полуавтоматическом режиме перемещается
вакуумная присоска, предназначенная для
захвата и перемещения устанавливаемого компонента из накопителя на место его монтирования на плате. Полуавтоматическое устройство монтажа комплектуется набором различных накопителей для компонентов (ленты, пеналы или плоские поддоны для расположения интегральных схем). Компоненты могут также браться из россыпи, для чего они помещаются в специальные ячейки. Устройство комплектуется персональным компьютером с ПО, определяющим последовательность установки и расположения компонентов на плате.
На производительность такого рода оборудования сильно влияет квалификация и опыт оператора. Как правило, полуавтоматы по установке компонентов позволяют монтировать до 400–500 компонентов в час.
Важная деталь: такое оборудование позволяет монтировать только SMD-компоненты. Выводные компоненты придется устанавливать вручную.
Наиболее сложным, дорогим и производительным оборудованием, используемым на данном этапе технологического цикла, являются автоматические установщики. Принцип их работы состоит в следующем: с помощью ПО файлы САПР транслируются в исполнительные программы, посредством которых монтажная головка устройства автоматически перемещает компонент из накопителя на место его монтирования на плате.
Основные характеристики автоматических установщиков компонентов:
- Производительность: может колебаться от минимально возможной — порядка 1,5 тыс. компонентов в час до очень высокой — более 50 тыс. компонентов в час. 40–50 тыс. установленных компонентов в час является пределом для самых крупных российских заводов.
- Номенклатура устанавливаемых компонентов: от ограниченного числа чипов и микросхем, наиболее простых для установки, до самых сложных компонентов, таких как чипы 0402 и 0201, ИС с шагом выводов менее 0,6 мм (fine-pitch) и корпусов с шариковыми выводами (BGA). Наиболее дорогостоящее оборудование позволяет монтировать не только SMD, но и некоторые выводные компоненты.
- Максимальная величина формата монтируемой платы при использовании групповой заготовки. Эта величина может достигать значения 12x18 (457x508 мм).
В некотором наиболее сложном оборудовании предусмотрена возможность использования производственной мощности установщика для выполнения дозирования материалов. Для этого вместо головки, устанавливающей компоненты, в автомате используется специальная дозирующая головка.
Как и для любого автоматического оборудования, в автоматах-установщиках большое значение имеет используемое ПО и его возможности. Можно отметить следующие функции ПО:
- возможность оптимизации исполнительной программы установки компонентов с точки зрения наиболее короткого перемещения головки;
- симулирование работы оборудования, позволяющее вычислять время сборки продукта без реального запуска автомата;
- сбор статистической информации о важнейших параметрах работы оборудования;
- возможность отбраковки помеченных бракованных плат;
- защита при помощи пароля.
Выбор оборудования, которое будет использоваться на данном этапе, необходимо проводить исходя из особенностей конструктива платы и производительности участка. При лабораторном производстве оптимально использование полуавтоматов, которые просты в управлении, сравнительно недороги (примерно 15–18 тыс. долл.), снижают утомляемость оператора, значительно превышают производительность оператора. При больших объемах производства необходимо использование автоматов, которые помимо увеличения производительности повышают качество изделия и снижают вероятность ошибок.
4. Пайка (оплавление припойных паст и пайка волной)
Пайка компонентов, установленных на плате, в зависимости от применяемой технологии может проводиться методом оплавления припойных паст и пайкой волной припоя.
Для проведения пайки оплавлением используются различные способы, самыми распространенными из которых являются конвекционная пайка, которая осуществляется горячим воздухом, и ИК-нагрев.
Конвекционная пайка реализуется в камерных или конвейерных печах. В первом случае отработка профиля пайки осуществляется путем изменения температуры внутри камеры со временем, а во втором — перемещением платы по конвейеру через несколько зон печи — через зоны нагревания, затем через зоны охлаждения, каждая из которых имеет свою температуру. Как правило, максимальная температура, при которой происходит непосредственно оплавление пасты, составляет 210–220 °C. Плата находится в печи при максимальной температуре в течение всего нескольких секунд, после чего производится ее охлаждение.
В ряде случаев применяется пайка в инертной среде, при которой осуществляется впуск азота в рабочую область печи. Эта операция используется для сведения к минимуму окислительного процесса. Однако необходимо проанализировать целесообразность этой операции. В случае, если процесс пайки длится не очень продолжительный промежуток времени (4–5 минут), припой просто не успеет окислиться, так как в его состав входит флюс, обеспечивающий растворение окислов на поверхности частиц порошка припоя. К тому же пайка в инертной среде потребует большого расхода азота, что повлечет за собой использование азотной станции, а это означает существенные дополнительные расходы.
Использование азотной среды при конвекционной пайке оправдано только в условиях серийного производства при изготовлении сложных модулей, требующих высокого качества исполнения.
Приведем значение некоторых ключевых параметров печей конвекционной пайки.
Для конвейерных печей имеет значение ширина конвейера (до 460 мм), для камерных — площадь рабочей области (до 350x500 мм). Максимальная рабочая температура может достигать 350 °C. Количество зон колеблется от
3 зон нагрева и 1 зоны охлаждения в небольших печах, применяемых в мелкосерийном производстве, до 12 зон нагрева и 4 зон охлаждения в больших промышленных установках. Длина печи может быть от 1 до 6 метров.
Что касается ПО, которое может поставляться вместе с печью оплавления, то здесь одним из основных свойств является возможность сохранения и вызова файлов с термопрофилями паечных процессов, которые могут быть реализованы на данной установке. Кроме того, возможно выполнение следующих функций:
- сбор и хранение информации о параметрах паечного процесса;
- контроль заданного температурного режима;
- создание системы подсказок.
Пайка волной припоя может использоваться для монтажа как выводных, так и SMD- компонентов. Основной частью установки является конвейер, по которому перемещается плата, омываемая снизу двойной волной припоя.
Двойная волна применяется по следующим причинам. Из-за наличия сил поверхностного натяжения и отсутствия смачиваемости пластмассового корпуса элемента припоем вблизи элемента образуется «тень», в которой отсутствует смачивание припоем выводов. Эта проблема особенно актуальна для высоких корпусов. Обычная волна не обеспечивает пайку всех выводов SMD-компонентов вследствие такого «теневого эффекта». Кроме того, обычная волна часто создает пайки с излишками припоя, что приводит к появлению перемычек между выводами компонентов. В установках двойной волны эти недостатки отсутствуют.
Еще одной важной частью установки пайки волной припоя является флюсователь. Это устройство должно обеспечить равномерное нанесение флюса на поверхность платы. Среди нескольких методов, которыми осуществляется эта операция, выделим флюсование разбрызгиванием и пенное флюсование.
Применение опции пайки в среде азота при пайке волной является гораздо более оправданным, чем при конвекции, а подчас и необходимым. Процесс окисления при пайке волной идет гораздо активнее, а расход азота при этом будет значительно меньше.
Основными параметрами, которыми определяется класс установки пайки волной и сфера ее использования, являются следующие:
- максимальная ширина платы (до 500 мм);
- максимальная высота компонентов на верхней стороне платы (100–150 мм);
- вместимость ванны с припоем (от 100 до 800 кг);
- наличие возможности регулировки угла наклона конвейера.
5. Ручные операции
Какой бы уровень автоматизации ни был реализован на производстве, ручного труда избежать не удастся. При ручном и полуавтоматическом характере производства работа операторов используется на всех этапах цикла. Автоматическая линия предполагает работу оператора на этапе визуальной инспекции после установки компонентов, пайки в печи оплавления и пайки волной, на этапе установки выводных компонентов и ручной досборки.
Рабочее место оператора, выполняющего операцию установки компонентов, должно быть обеспечено набором ручного инструмента для захвата компонентов (пинцеты, вакуумные захваты), увеличительным стеклом, желательно с подсветкой (для меньшего утомления зрения оператора), а также местом для размещения плат в накопителях. Рабочее место, на котором будут выполняться операции контроля и ручной пайки, должно быть укомплектовано рабочей станцией.
Заключение
В статье рассмотрены только основные технологические операции. Здесь не были освещены вопросы формовки и обрезки выводов THT-компонентов, комплектации компонентов, сушка ПП и компонентов в среде азота перед началом технологического цикла, внутрисхемный и функциональный контроль, а также другие операции, которые могут быть проведены на сборочно-монтажном производстве.
Владислав Клейменов
fregat-polo@mtu-net.ru
|